What is Lean management in a nutshell?
Lean management is one of the methods and tools whose main objective is continuous improvement, becoming better.
In other words, it serves to move an organisation forward by making small improvements over time.
We also find the principles of continuous improvement in other management systems such as ISO, MASE, the EFQM (European Foundation of Quality Management) model... Of course, no company's management system is perfect.
However, they all aim to correcting a problem rather than ignoring it or even anticipating it.
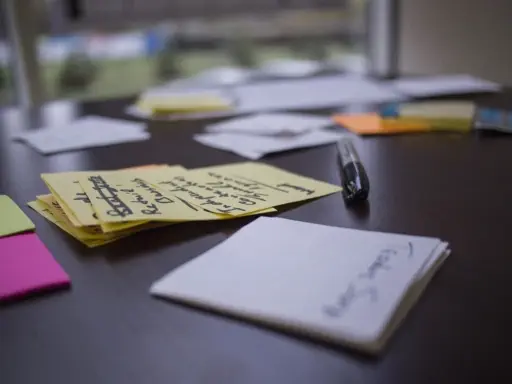
Historically, lean management has its roots in the 1970s in the Japanese automotive industry at Toyota. It is based on a fundamental principle in the long term: reduce waste to keep the essentials.
For example, when you notice that you are late, it is no longer possible to make up for lost time. So you have to anticipate obstacles. In the same way, when your family grows, you have to anticipate changes: travel arrangements, car size, food, etc. Well, it's the same thing when you go from a company of 10 to 30 people, from 30 to 100, etc. Like any entrepreneur, you have to ask yourself some basic questions.
In other words, it is necessary to organise itself with a methodology to improve the way it produces, to satisfy its customers by creating value and to take into account the well-being of its employees.
You can find the principles of lean management in the 14 principles of the Toyota model according to Jeffrey Liker.
The benefits of Lean management
As we have said, the final objective is the continuous improvement of the company's performance. This includes :
- Regularly listening to its internal (e.g. employees) and external (e.g. customers) customers
- The search for improvements in its working methods and therefore in the production of products or services, through the reduction of deadlines, stocks, optimised transport management, internal and external communication, etc.
- The development of knowledge, technical and human skills of employees through training to increase the quality of products and/or services
- Involvement and motivation of its employees through good working conditions to give the best
It is therefore relatively simple to integrate lean management into a quality approach.
The disadvantages of Lean management
The principles of lean management are virtuous for the company. However, it must not abuse this system. The primary objective is to be efficient without forgetting the well-being of employees, particularly since the arrival of generations Y and Z who are open to more agility and creativity in company projects.
Your human resources are key, so this is not a method based solely on improving productivity. The duality between continuous improvement and respect for people is real. Focusing on processes without taking into account people will be a source of failure in the implementation of lean depending on the sector, the company culture and the country.
Lean management tools
Unlike other management systems which do not always recommend tools to go beyond the concept.
Lean management presents several tools or methods of continuous improvement that can be applied in practice.
Some examples are given below:
The Kaizen is a state of mind that must come from the management. It aims at the continuous improvement of the daily work organisation. The participation of employees is a force for step-by-step progress.
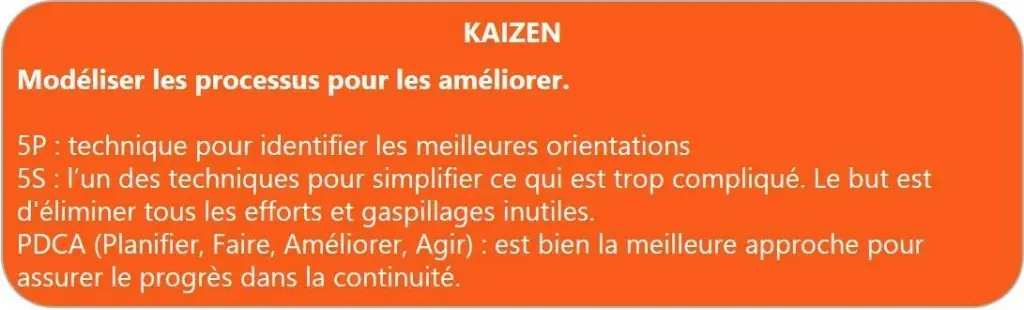
The Kanban is a method that aims to balance production with demand. In short, lean production management with minimum stock. It is especially suitable for industry.
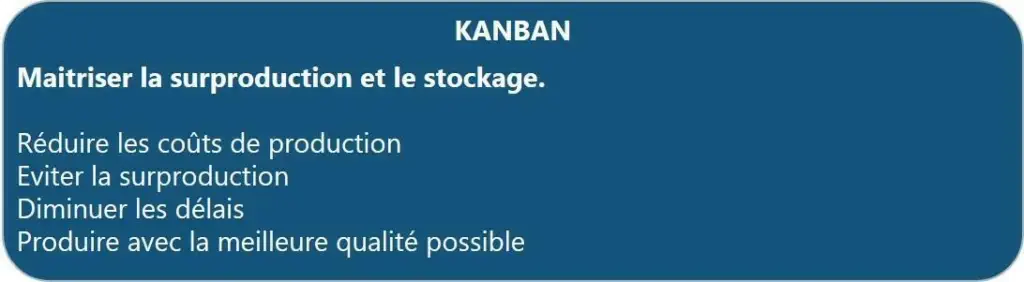
The 5S The 5S method is a Japanese technique for designing work spaces: organization, cleanliness, safety, noise, storage, etc. (see article The 5S method: what is it for?)
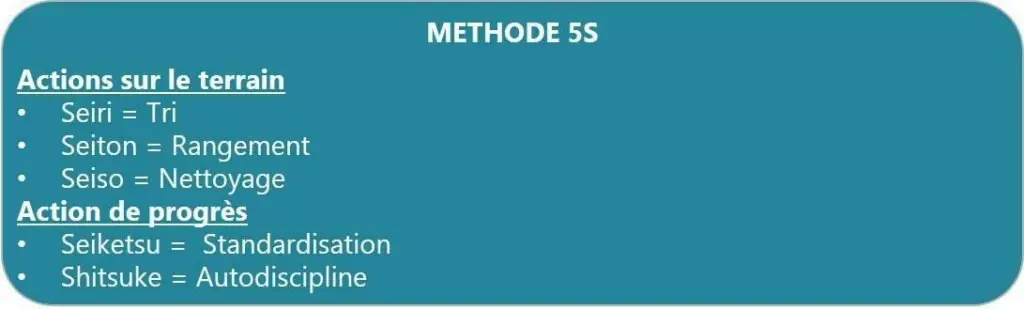
The Six Sigma is to understand customer needs in order to improve overall processes and measure performance to support product quality.
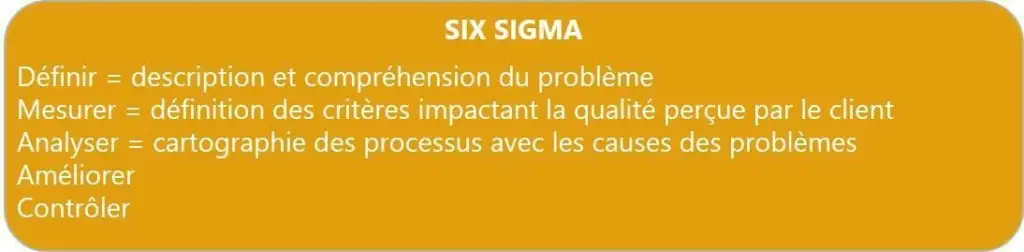
Our advice: Conclusion
There are many management systems. What they have in common is that they contribute to improving the performance of an organisation through effective people, tools and working methods to limit the risks of :
- Waste of time and money in research, waste, material management, ...
- Obsolescence of staff skills
- Dissatisfaction of internal and external stakeholders, in particular customers
- Duplication and/or dissatisfaction with work done due to lack of knowledge of company rules
- Health, safety and environmental impacts
- ...
The productivity and performance needs of the company must take into account the employees who must be involved and motivated. Lean management must therefore have a positive impact on the company and enable the whole to progress despite organisational changes. As Mark Twain said Continuous improvement is better than delayed perfection ".